inclined belt conveyor
An inclined belt conveyor is a precision-engineered material handling solution designed to transport products efficiently across elevation changes. These systems are built with high-quality components, including reinforced belts, heavy-duty drive motors, and precisely aligned pulleys, ensuring seamless operation even in demanding environments. Key design considerations include customizable incline angles, belt types (smooth or cleated), and optional sidewalls for material containment. These conveyors are engineered to handle a wide range of materials, from bulk commodities to delicate items, while maintaining high throughput rates. We emphasize durability, low maintenance, and adaptability, offering tailored solutions to meet the specific operational requirements of industries such as mining, agriculture, manufacturing, and logistics.
1. Efficient Material Handling
- Continuous Transport: Inclined belt conveyors enable smooth and continuous movement of materials, allowing for uninterrupted workflows.
- High Throughput: These systems can handle large volumes of materials efficiently, making them suitable for heavy-duty applications.
2. Versatility
- Various Materials: Inclined belt conveyors can transport a wide range of materials, including bulk materials like grains, sand, or gravel, as well as boxes and cartons in warehouses.
- Adjustable Design: The inclination angle and belt speed can often be adjusted to suit specific needs, allowing for flexible handling of materials with different shapes, sizes, and weights.
3. Space-Saving Design
- Vertical Transport: Unlike horizontal conveyors, inclined belt conveyors allow vertical movement, saving floor space in facilities.
- Compact Layout: Their design helps maximize space by utilizing the facility’s height instead of the floor area, making them ideal for locations with limited space.
4. Enhanced Safety
- Reduced Manual Handling: By automating material transport on inclines, these conveyors reduce the need for manual lifting and carrying, minimizing the risk of injuries.
- Secure Material Transport: Equipped with special belts (like cleated or textured belts), inclined conveyors prevent materials from slipping, ensuring they stay securely in place.
5. Energy Efficiency
- Low Power Consumption: Inclined belt conveyors often use energy-efficient motors and designs to transport materials, consuming less energy than other methods of moving materials vertically.
- Cost Savings: Reduced power requirements mean lower operational costs over time.
6. Increased Productivity
- Reduced Transport Time: These conveyors reduce the time needed to move materials across different levels, speeding up production and enhancing productivity.
- Automation-Compatible: They integrate well into automated production lines, minimizing the need for manual intervention and increasing overall process speed.
7. Customizability and Specialization
- Tailored to Application Needs: Inclined belt conveyors can be customized with cleats, sidewalls, or special belts to handle specific materials or work in particular environments.
- Various Configurations: They come in different configurations (such as Z-type, L-type, and C-type), allowing them to fit into unique workflows and production layouts.
8. Reduced Maintenance Costs
- Durable and Low Maintenance: Inclined belt conveyors are generally durable and require less maintenance than other systems, which can reduce overall operational costs.
- Simplified Repairs: When maintenance is necessary, belt replacement and repairs are often straightforward, limiting downtime.
9. Improved Workflow and Layout
- Integration with Other Systems: They can seamlessly integrate with other conveyor systems, hoppers, or discharge chutes, optimizing workflow in production or distribution lines.
- Better Facility Organization: Inclined conveyors allow for a more organized and efficient workspace by providing designated routes for materials, reducing clutter and congestion.
10. Reduced Environmental Impact
- Environmentally Friendly Materials: Many conveyors now use belts made from eco-friendly materials, making them more sustainable.
- Waste Reduction: Their efficiency and reliability reduce the risk of spillage and waste, helping to minimize material loss.
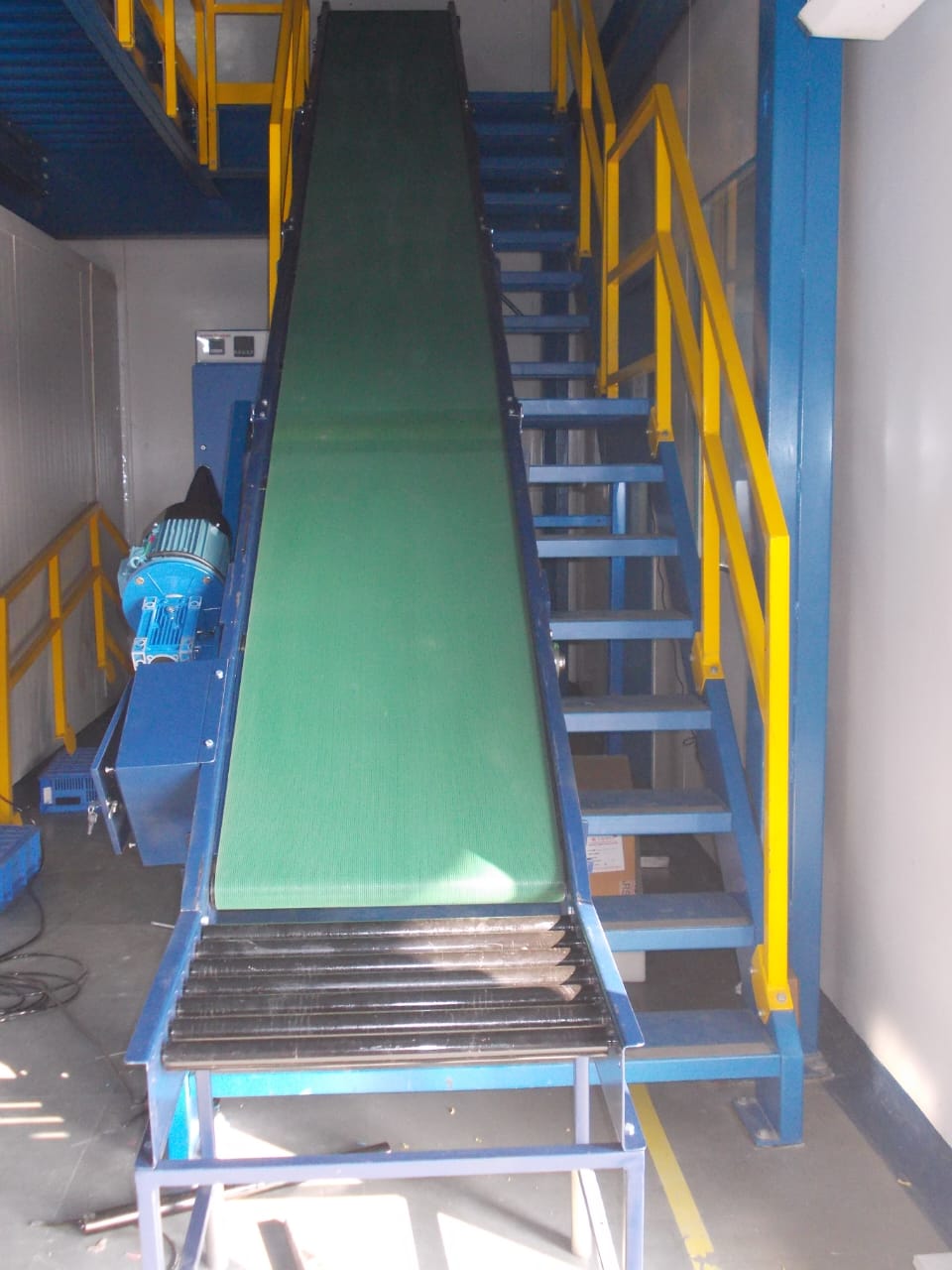