inkjet printing conveyor
An Inkjet Printing Conveyor is a specialized conveyor system designed for integrating inkjet printing operations. It features a moving belt that transports products under an inkjet printer, allowing for on-the-go printing of labels, barcodes, batch numbers, expiration dates, or other markings directly onto the items. This type of conveyor is commonly used in industries such as packaging, food and beverage, pharmaceuticals, and manufacturing. The system ensures precise alignment and speed control to match the printing process, enabling high-quality, continuous printing on a variety of surfaces and product types.
BENEFITS –
1. High-Speed Production
- Continuous Operation: Conveyor-based inkjet systems can print on products as they move along the conveyor, eliminating the need for stopping or slowing down the production line.
- Increased Throughput: High-speed inkjet printers can operate in sync with fast conveyor belts, allowing for a high volume of products to be printed in a short time.
2. Versatility and Flexibility
- Variety of Substrates: Inkjet printers can print on many different materials, including plastics, metals, glass, and cardboard, making them versatile for various industries.
- Customization Capabilities: Inkjet systems allow for on-demand changes to printed information, such as text, images, barcodes, dates, or serial numbers. This makes them ideal for custom orders or frequently changing product information.
- Variable Print Heights and Angles: Many conveyor-based systems can adjust to print on products of various sizes, shapes, and orientations, even on uneven or curved surfaces.
3. Cost Efficiency
- Reduced Material Waste: Since inkjet printing is a non-contact process, it minimizes damage to the product and reduces wasted materials.
- Lower Inventory Needs: Instead of stocking pre-printed labels or packaging, companies can print information directly on products, saving on label costs and storage space.
- Reduced Labor Costs: Automated inkjet printing on conveyors reduces the need for manual labeling or handling, which can lower labor expenses and increase productivity.
4. Precision and Consistency
- Accurate Placement: Conveyor-based inkjet printers can be precisely calibrated to print in the same position on each product, ensuring uniformity and quality control.
- Consistent Quality: With digital inkjet technology, the same high-quality images or text can be printed repeatedly without variation, crucial for brand integrity.
5. Environmentally Friendly
- Reduced Labeling Waste: Direct inkjet printing on products or packaging reduces the need for extra materials like labels, adhesive, and backing paper, which are often non-recyclable.
- Low Power Consumption: Inkjet printing technology generally uses less power compared to other printing methods, reducing overall energy consumption.
6. Easy Maintenance and Operation
- User-Friendly Interface: Many conveyor-based inkjet printers come with intuitive software that makes it easy to change settings or adjust print designs.
- Low Maintenance Needs: Modern inkjet printers often have self-cleaning nozzles and easy-to-replace ink cartridges, leading to minimal downtime and maintenance costs.
7. Data Integration and Traceability
- Real-Time Data Integration: Inkjet conveyor systems can integrate with databases or ERP systems to dynamically pull data, such as batch numbers, expiration dates, and serial numbers.
- Enhanced Traceability: By printing detailed product information directly onto products or packaging, these systems facilitate better tracking throughout the supply chain, which is crucial for industries like food and pharmaceuticals.
8. Compliance with Regulatory Standards
- Meets Industry Standards: Inkjet conveyors are widely used in industries with stringent labeling requirements, such as food, beverage, pharmaceuticals, and electronics. They allow companies to stay compliant with regulations by printing clearly readable information, such as lot numbers and expiration dates.
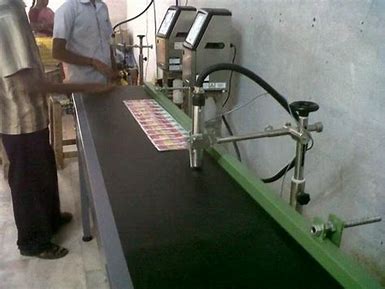