Motorized Roller Conveyor
equipped with electric motors that move the unit loads (pallets or boxes) in a controlled way. Motorized roller conveyors are made up of a series of rollers that support the load and propel it along a circuit
1. Enhanced Efficiency and Speed
- Reduced Manual Handling: Motorized roller conveyors eliminate the need for workers to manually move heavy or large items, increasing productivity and minimizing strain.
- Higher Throughput: The controlled, continuous movement allows for faster processing and transportation, speeding up operations.
- Adjustable Speed Control: Many systems come with speed control options, enabling precise handling of goods based on requirements.
2. Energy Efficiency
- On-Demand Motorization: Unlike traditional conveyors that run continuously, motorized roller conveyors can be programmed to run only when needed, reducing energy consumption.
- Low Power Requirement: Motorized rollers often use low-voltage motors, which consume less power than larger traditional conveyor motors.
3. Scalability and Modularity
- Modular Design: These conveyors can be easily expanded, modified, or reconfigured to suit the changing needs of a facility, making them a flexible solution.
- Customizable Length and Layout: They can be adapted to various lengths and layouts, including curves and inclines, which allows for integration into diverse production lines.
4. Improved Safety
- Reduced Accidents: By automating material movement, the conveyor system minimizes human handling, reducing the risk of accidents and injuries.
- Smart Start/Stop Functions: Many systems can detect the presence of items, starting and stopping automatically, which prevents accidents due to unexpected starts.
5. Minimal Maintenance Requirements
- Reduced Wear and Tear: With fewer moving parts than traditional conveyor systems, motorized roller conveyors experience less wear, reducing downtime and maintenance costs.
- Easily Replaceable Components: Modular design allows for quick replacement of individual rollers or motors without the need to disassemble large sections of the conveyor.
6. Precise Material Control and Sorting
- Automated Staging and Accumulation: Motorized roller conveyors allow items to be accumulated (stopped and queued) without manual intervention, making them ideal for sortation and staging processes.
- Smart Sensor Integration: Many systems integrate sensors to detect and control the flow of materials, allowing for precise, automated sorting and routing.
7. Reduced Noise and Vibration
- Quieter Operation: Due to the low-power motors and roller-based movement, these conveyors produce less noise than traditional belt or chain conveyors.
- Reduced Vibration: The rollers minimize vibration, providing a smoother transport system that reduces wear on both the conveyor and the items being transported.
8. Cost-Effectiveness Over Time
- Longer Service Life: Reduced wear, lower energy consumption, and minimal maintenance make motorized roller conveyors a cost-effective solution for the long term.
- Lower Operational Costs: The energy savings and reduced need for manual labor contribute to overall cost reduction in operations.
9. Environmentally Friendly
- Energy-Efficient Motors: Lower energy consumption contributes to a smaller carbon footprint.
- Quiet Operation: Reduced noise pollution makes motorized roller conveyors more suitable for environmentally conscious workplaces.
10. Easy Integration with Automated Systems
- Adaptability to IoT and Industry 4.0: Many modern systems can be integrated into IoT networks, allowing them to be controlled and monitored remotely, ideal for smart factories.
- Compatibility with Robotic and Automated Systems: These conveyors work seamlessly with automated pick-and-place robots, sorting systems, and other industrial automation equipment.
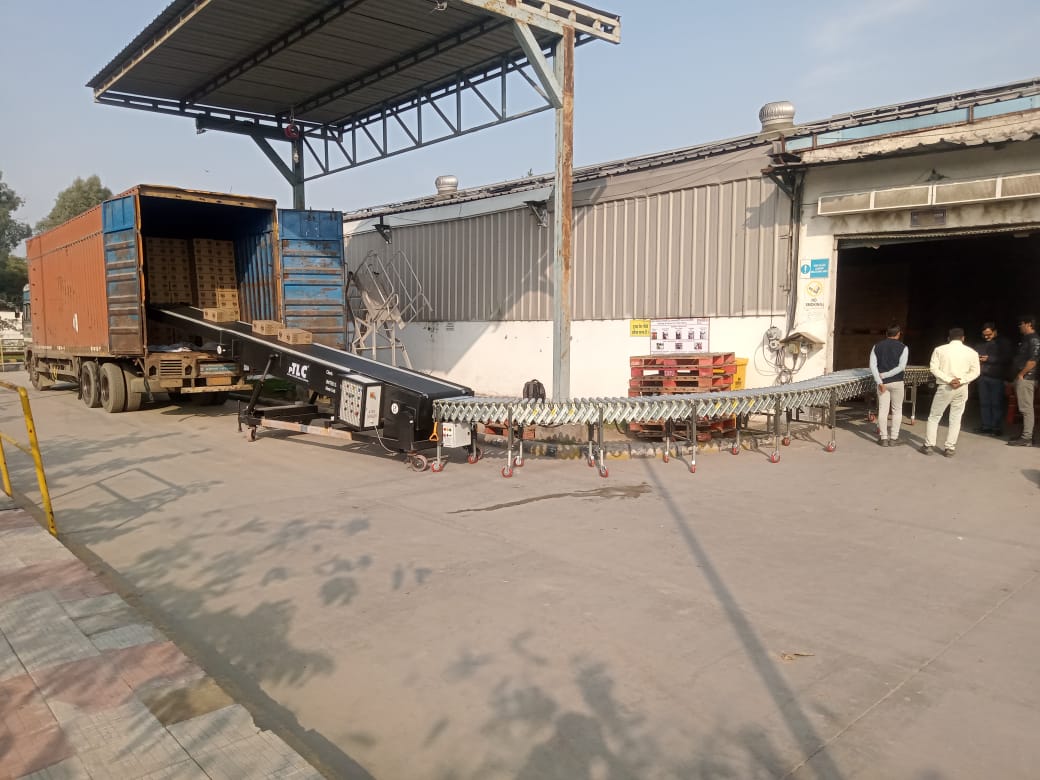