Packing Belt Conveyor
A Packing Belt Conveyor is a conveyor system used primarily in packaging operations to transport products during the packing process. It features a continuous, motor-driven belt that moves items from one station to another, typically for tasks like sorting, inspecting, labeling, or packaging. This conveyor is often found in industries such as food processing, pharmaceuticals, and manufacturing. It helps streamline the packing process by reducing manual handling, improving efficiency, and maintaining a steady workflow. The belt material can vary depending on the product type and industry requirements
1. Increased Efficiency and Productivity
- Packing belt conveyors move items smoothly from one station to the next, enabling faster and more consistent processing.
- Automation of item transportation reduces manual handling, allowing employees to focus on more complex tasks, boosting overall productivity.
2. Reduced Labor Costs
- With fewer hands-on tasks needed for moving items, packing belt conveyors minimize the need for manual labor.
- Reduced labor means lower wage expenses and less strain on workers, leading to fewer injuries and time off, indirectly saving on labor costs.
3. Improved Safety
- Reduces risks of injuries from heavy lifting, repetitive movements, or carrying loads across long distances.
- Well-designed conveyor systems often have safety features to avoid accidents, like guards and emergency stop buttons, ensuring safer operations.
4. Consistent and Controlled Flow of Goods
- Maintains a steady flow of goods on the production line, ensuring no bottlenecks or inconsistent processing times.
- Helps keep the packing line organized by moving items in a controlled and predictable manner, reducing errors.
5. Scalability and Flexibility
- Packing belt conveyors are customizable and can be adjusted or extended as business needs grow.
- They can handle a wide range of products, from small items to bulkier packages, offering versatility for various types of goods and packaging setups.
6. Enhanced Quality Control
- Conveyors enable precise control over the speed and direction of items, which helps standardize the quality of packaged goods.
- Additional inspection or quality control points can be integrated into the conveyor line, allowing easy detection and removal of defective items.
7. Space Optimization
- Packing conveyors can be designed to fit in narrow or compact spaces, making the most of the available area.
- Multi-level or modular conveyors save on floor space and can be configured to maximize workflow efficiency.
8. Improved Order Accuracy and Customer Satisfaction
- Reduces errors by automating much of the packing and movement process, leading to more accurate order fulfillment.
- Faster, more accurate packing and shipping contribute to shorter lead times and improved customer satisfaction.
9. Reduced Operational Costs
- Automated conveyor systems consume less power than manual transportation, lowering energy costs.
- With fewer operational disruptions and maintenance needs, these systems can reduce long-term operational expenses.
10. Environmentally Friendly
- Packing conveyors can be designed with energy-efficient motors and eco-friendly materials.
- Automation and optimization also reduce waste and resources, contributing to a greener production process.
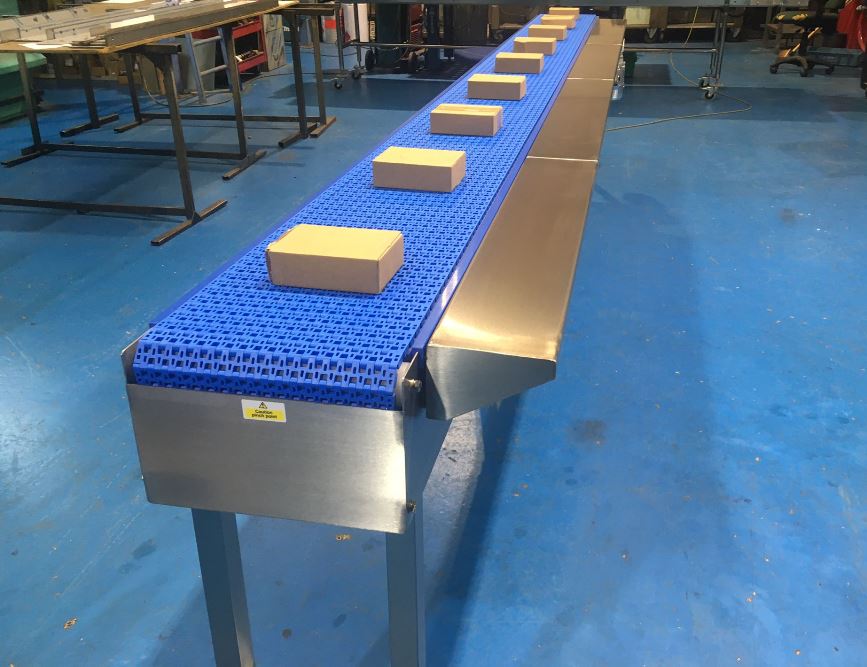