slat chain conveyor
A Slat Chain Conveyor is a type of conveyor system that utilizes a series of connected slats or links made from materials such as plastic or metal. These slats are designed to create a continuous surface for transporting various products, including bulky, heavy, or oddly shaped items. Slat chain conveyors are often used in manufacturing and assembly operations, as well as in packaging and material handling applications.
BENEFITS –
1. Versatile Material Handling
- Slat chain conveyors can handle a wide range of materials, including heavy, abrasive, and fragile items, making them suitable for industries like automotive, food processing, and manufacturing.
- They can transport both solid and liquid materials and are ideal for irregularly shaped or oversized items that might be difficult for other conveyor types.
2. Durability and Strength
- Made from robust materials like stainless steel or plastic, slat chains can withstand harsh conditions and high loads without wear or damage.
- They’re ideal for handling heavy-duty products in environments that may be exposed to temperature fluctuations, moisture, or corrosive substances.
3. Flexibility in Layout Design
- Slat chain conveyors can be designed in various layouts, including straight, inclined, curved, or spiral paths. This adaptability allows for optimization of floor space.
- Their modular structure allows for easy integration into existing systems and flexibility for future expansion.
4. Precise Product Handling and Stability
- Slat chains provide a stable and consistent platform for items, reducing product slippage, which is crucial for delicate or precise handling applications.
- They’re beneficial in assembly lines where exact positioning is needed since products can be positioned accurately on the slats.
5. Ease of Maintenance
- Slat chains are easy to maintain and clean. Damaged slats or chains can often be replaced individually without dismantling the whole system, which minimizes downtime.
- Their robust design leads to reduced maintenance costs and longer service life.
6. Customizable for Specific Applications
- Slats can be customized with different surfaces (such as smooth or textured) to suit particular product requirements. For example, food-grade slats can be used in the food industry, while high-friction surfaces may be used for packaging or transport.
- Accessories like side guards, stops, or sensors can be integrated easily for additional functionality.
7. Low Operational Cost
- With a relatively simple design, slat chain conveyors have fewer moving parts compared to other conveyor types, leading to lower energy consumption and operational costs.
- Their efficiency and minimal downtime add up to reduced long-term costs.
8. Enhanced Safety
- Slat chain conveyors are safer for operators because the slats cover the chain, reducing the risk of items getting caught or entangled.
- They are often equipped with features like emergency stop systems and guards, enhancing workplace safety.
9. Suitable for High-Temperature Applications
- Due to their durability, slat chain conveyors can operate under high-temperature conditions, which makes them ideal for applications such as transporting hot items in metal fabrication or glass manufacturing industries.
10. Efficient for Accumulation and Sorting
- They’re ideal for accumulation applications, where items can be stored on the conveyor until they are ready to be moved. This is particularly useful in packaging and bottling lines.
- Sorting systems can also be added, which is beneficial for logistics and warehousing applications.
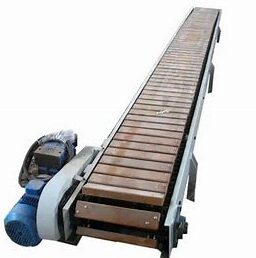